SELLINO PILOTA
su VN1700
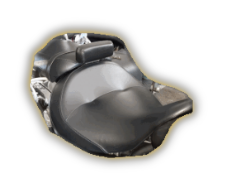
INTRO
Siamo abituati a vedere moto con schienalini per i passeggeri, ma ci siamo mai soffermati a pensare perché solo i nostri passeggeri devono godere di questo privilegio?
Era un po che cercavo un idea per costruirmi uno schienalino per me, cosi ho iniziato ad analizzare la mia moto per capire come si sarebbe potuto fare e finalmente ho trovato una soluzione semplice e molto furba.
Il seguente progetto è stato realizzato su una Kawasaki VN1700, ma sfruttando il concetto si può adattare ad altri tipi di moto che hanno la fortuna di avere il sellino diviso tra driver e passeggero.
Analizzando il semplice sellino del guidatore ho notato che lo schienalino era appoggiato al telaio tramite un supportino metallico molto rigido. Cosi le mia mente ha cominciato a ragionare intorno a questo pezzo di metallo, trovando poi la soluzione al mio scopo finale.
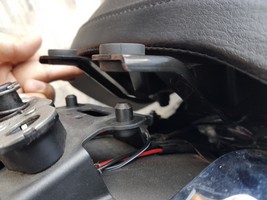
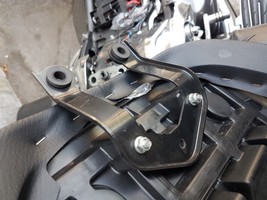
Cerchiamo di analizzare punto per punto, in modo da entrare dentro al progetto e capirele motivazioni della realizzazione.
Iniziamo a studiare il progetto
Togliere quel supporto e costruirne uno uguale sarebbe stato troppo problematico; si rischiava di dover smontare la fodera per svitare i dadi di supporto e di prendere delle misure sbagliate ( non è facile riprodurre quella forma piegata).
Cosi ho pensato ad un supporto da dover aggiungere, forando direttamente la staffa senza doverla smontare.
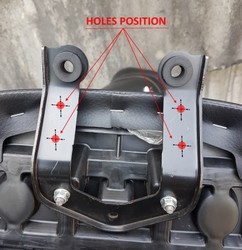
Ho iniziato a fare delle prove con un sottile nastrino di alluminio , piegabile facilmente a mano e ho cercato di trovarne una forma logica e funzionale.
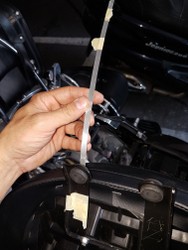
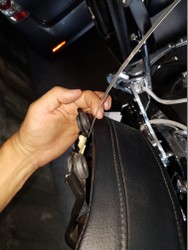
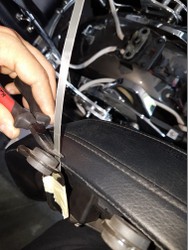
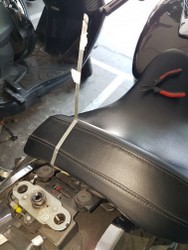
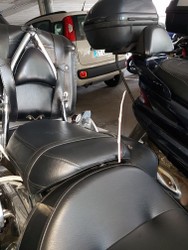
Trovato le pieghe consone allo scopo , ho riportato gli angoli su carta e ho iniziato a studiarne la forma a CAD.
Ho pensato alla foratura da eseguire sul pezzo originale e ho riportato tali fori ipotizzati sul progetto, pensando a costruire anche una sesta che mi sarebbe poi servita per tracciare i fori sullo schienalino.
Insomma modellando al computer ho simulato come sarebbe stato il mio schienalino da montare sulla staffa esistente, dimensionandolo opportunamente e creando poi li sviluppi delle lamiere necessarie.
Supporto di lamiera
Pensata la forma ed eseguito il progetto a CAD ho fatto tagliare al laser il pezzo di lamiera sviluppato di acciao inox 316 spessore 3mm ( forse un po esagerato... 2mm è piu che sufficiente, ma mi piace stare tranquillo).
Ricordo che gli acciai migliori per questo genere di cose sono il AISI308 e il AISI316 entrambe molto resistenti alla corrosione e il secondo (316) nato apposta per l'uso marino, e quindi resistente al sale, senza dimenticare che entrambe sono piu facili da lucidare a specchio.
La forma l'ho studiata ritagliando un cartoncino e facendo varie prove sulla moto stessa ( purtroppo non ho foto , ma è semplice immaginarlo) e i fori sono stati ragionati e pensati anche per futuri utilizzi ( io abbondo sempre con i fori... non si sa mai).
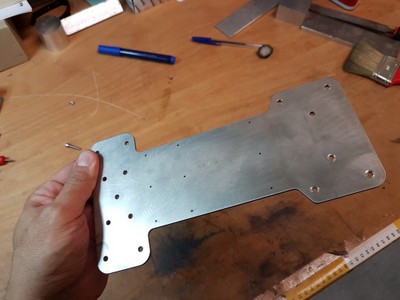
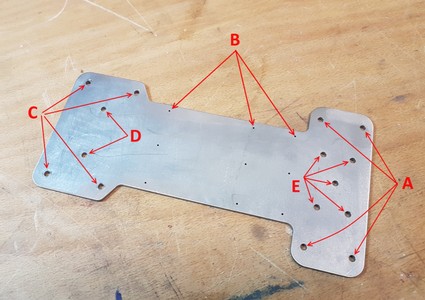
Come potete notare ci sono un po di fori. ora di seguito proverò a spiegarvi come li ho pensati:
fori "A" = Sono i fori che andrò a fare sul supporto originale del sellino.
fori "B" = Questi sono fori importantissimi, ma non fondamentali. Servono per segnare la piega da fare. In questo modo si evita di dover tracciare il pezz0 o doverlo segnare con matite o pennarelli, la piega andrà eseguita direttamente lungo i fori. Ne ho fatti 3 per ogni linea di piega.
fori "C" = sono i fori per montare lo schienalino imbottito.
fori "D" = lho pensati per eventialmente montare un logo avvitato o fissare una copertura imbottita nel caso lo schienalino desse fastidio al passeggero.
fori "E" = questi fori servono per nontare una sesta per poter tracciare i fori sul supporto del sellino originale ( vedi piu avanti come vengono utilizzati).
Prima di pensare a piegare la nostra lamiera, conviene procedere a una bella lucidatura delle superfici e una sbavatura grossolana per eliminare il piu possibile gli spigoli taglienti, ricordate che l'acciaio inox TAGLIA COME UN RASOIO.
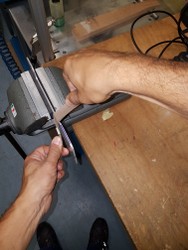
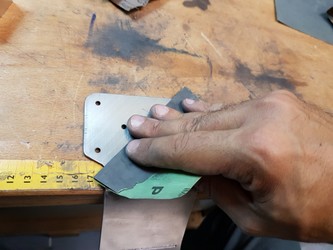
Piegare la lamiera
Piegare la lamiera è la cosa piu noiosa, perchè ci vuole lo spazio e gli strumenti, quindi se volete risparmiare qualcosa, vi spiego 2 tecniche.
La lamiera in oggetto presenta dei forellini da 1mm ( vedi figura sopra) ... quelli sono stati eseguiti per avere un riferimento di piega, sia lo facciate a macchina che a mano questi punti di riferimento vi verranno molto utili.
Come prima tecnica vi spiego come si può piegare della lamiera utilizzando una morsa da banco ( una bella morsa e fissata come si deve ad un buon tavolo da lavoro).
Procuratevi degli sfridi di metallo precisi da usare come supporti di piega, una morsa a vite o "strettoio a vite", un asta lunga.
Fissare la lamiera alla morsa ponendola in mezzo stile sandwich e facendola combaciare la linea dritta dei supporti con i forellini che abbiamo fatto. Tenete il "sanwich" appena stretto nella morsa ; aiutatevi con un martello per raddrizzare la lamiera e sistemarla nella corretta posizione.
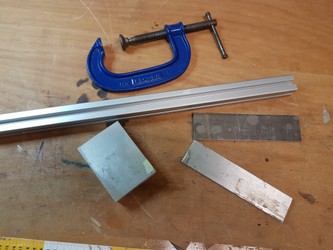
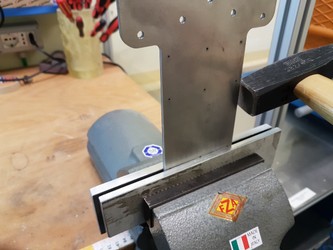
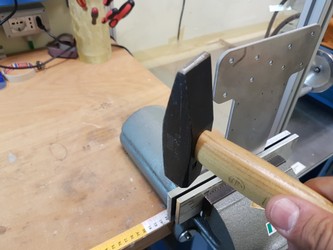
Stringete la morsa piu che potete e fissate una barra di forma quadrata o rettangolare alla lamiera dalla parte opposta di dove farete la piega utilizzando lo strettotio a vite.
Ora iniziate a piegare la lamiera, verificando l'angolo di tanto in tanto ( io per verificare gli angoli mi sono fatto un profilo in stampa 3D e di volta in volta verificavo la giusta piega, ma potete utilizzare anche un cartoncino )
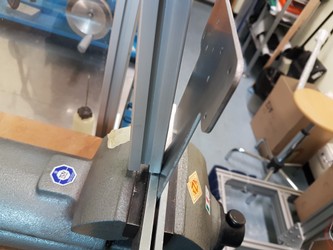
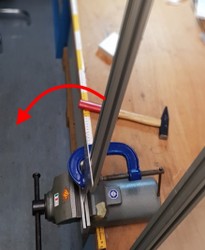
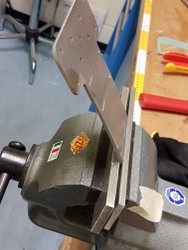
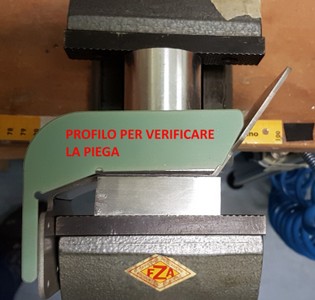
Se si vuole facilitare l'operazione di piegatura della lamiera e si ha a disposizione una fresa, di puo tracciare la linea di piega fresando via un po di materiale per facilitarne la piega a mano. Avendo scelto una lamiera da 3mm e volendo piegare la lamiera a mano, la mia è stata una scelta quasi obbligata, in realtà con una piegatrice professionale si piega senza problemi.
Ricordatevi di eseguire la scanalatura nella perte interna di piega, quindi nel nostro caso verranno eseguite 2 scanalature da una parte e una nell'altro lato.
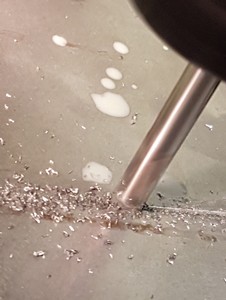
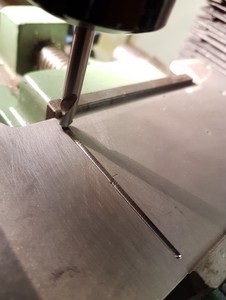
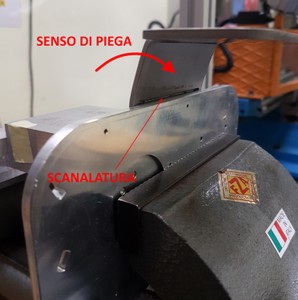
Procedere ora alla filettatura e svasatura dei fori, ponendo attenzione al lato corretto delle svasature. Usate i maschi da filettare in scala.
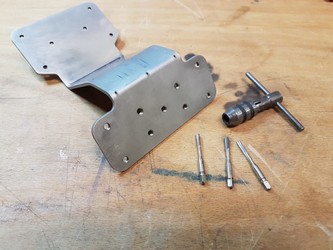
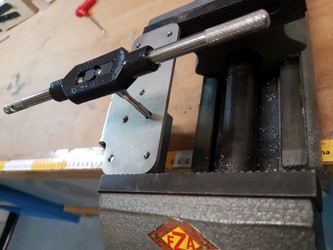
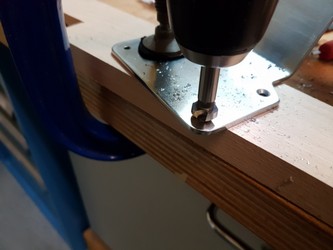
Foratura e test sul sellino della moto
Di seguito una breve descrizione di come eseguire i fori sul supporto dello schienalino.
Per prima cosa, mi sono procurato una sesta per facilitare la tracciatura dei fori. Ho posizionato la lamiera dello schienalino sul supporto del sellino e ho posizionato sopra la sesta. In questo modo la sesta mi dava l'esatta posizione dei fori che, essendo nella parte nascosta, potevo utilizzare per la tracciatura.
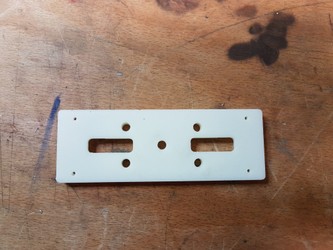
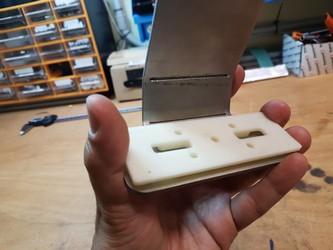
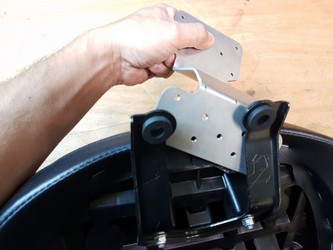
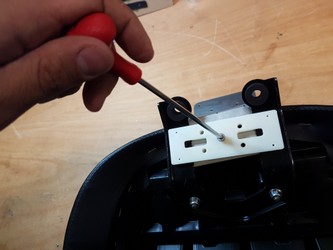
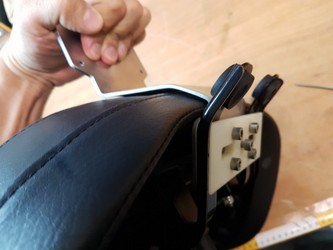
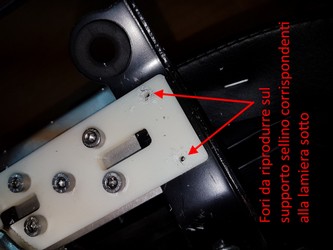
Posizioniamo saldamente la lamiera nella giusta posizione, aggiungendo anche una pinza a grip per tenere serrato con piu decisione.
Ora possiamo utilizzare il trapano per segnare i fori ( utilizziamo una punta piccola, come ad esempio una ø2mm).
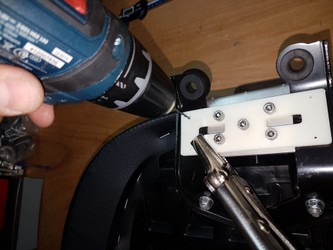
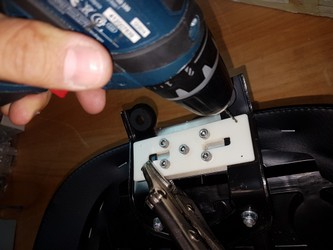
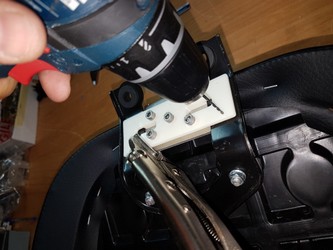
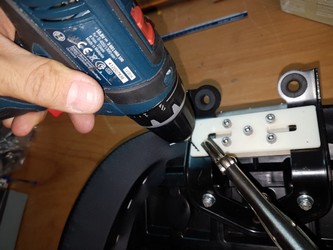
Una volta segnati i fori possiamo smontare tutto e procerede ad allargare i fori della dimensione delle viti : nel mio caso avendo filettato il supporto da M5 ho eseguito dei fori da ø5.1mm. Puliamo la sbavatura dei fori con un po di cartavetro e il nostro supporto è pronto per alloggiare lo schienalino.
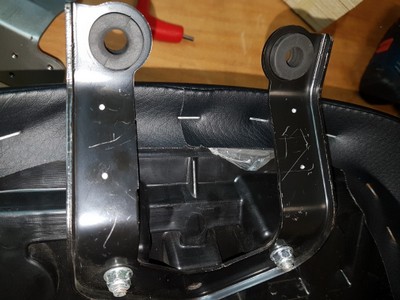
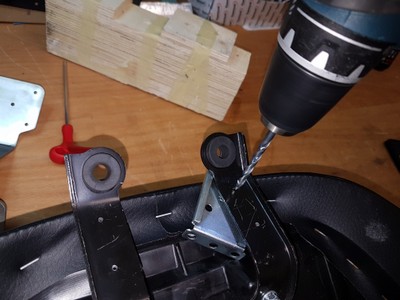
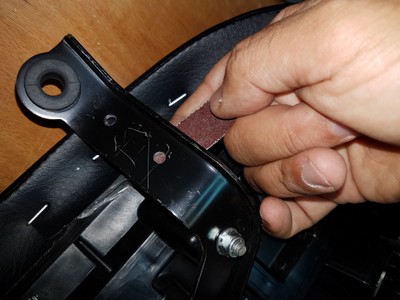
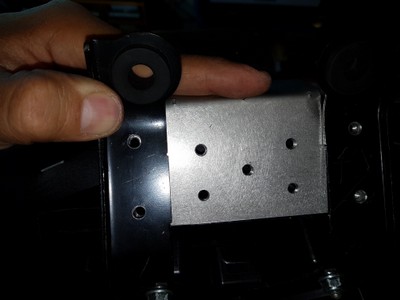
Costruzione cuscino
Per la costruzione del cuscino dobbiamo procurarci una lastra di plastica da tagliare della forma finale del cuscino: il materiale piu appropriato è il teflon , in quanto ha una struttura abbastanza rigida, ma allo stesso tempo e abbastanza morbido per poterlo graffettare quando si mette il rivestimento.
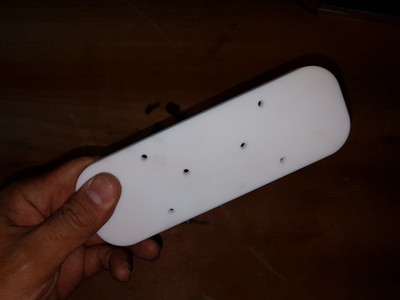
Per mezzo di un phon ad alte temperature ho cercato di scaldare la lastra di plastica dargli una leggera piega per seguire meglio il profilo della schiena, e dare quella senzazione di avvolgimento che ti stabilizzano durante la guida.
Per far ciò lo posizionata sulla morsa e lho scaldata per bene e piegata a mano , lavoro da fare delicatamente , basta una leggera piega.
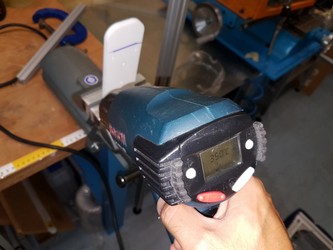
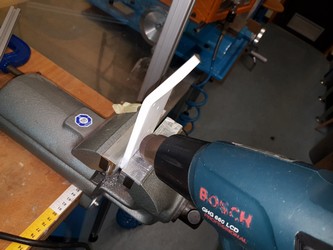
Per fissarla al supporto di lamiera , ho pensato a delle viti M4 svasate in inox (UNI5933) e per evitare di filettare la plastica ( che risulterebbe troppo fragile) ho deciso di inserire degli inserti da M4 affogati direttamente sulla lastra.
Posizionando la boccoca sulla vite e scaldandola con il phon ad altre temperature , è possibile pressare la boccola all'interno della lastra, semplicemente avvitando la vite.
Una volta raffreddato la boccola era rigidamente assemblata alla lastra.
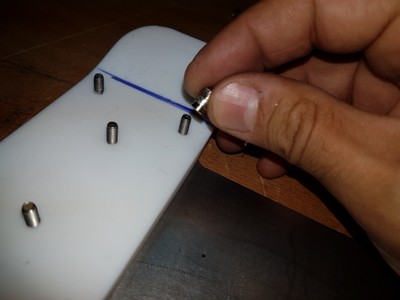
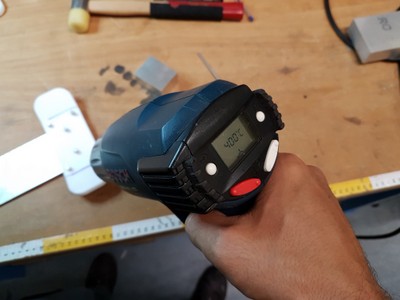
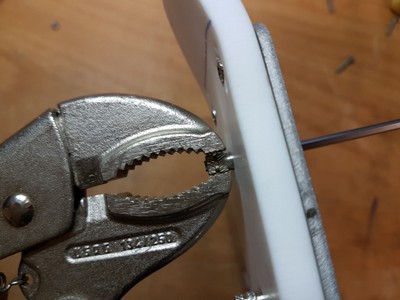
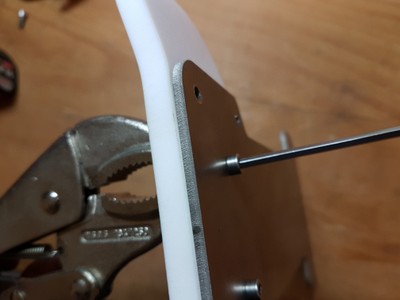
Successivamente ho ritagliato dei pezzi di neoprene che avevo , circa la forma del cuscino ( un po piu grandi a dire il vero ) e lìho incollati con del bostik sulla plastica . Una volta asciutta con l'aiuto di un taglierino molto affilato o ritagliato il bordo e ho paregiato le superfici con una cartavertro muovendola con passaggi delicati sul neoprene.
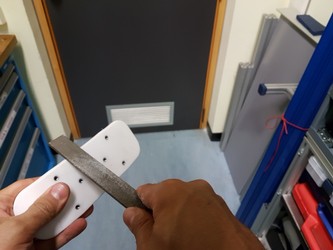
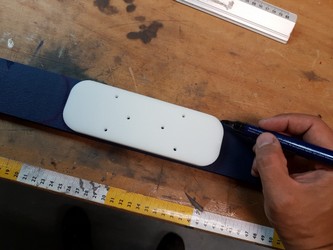
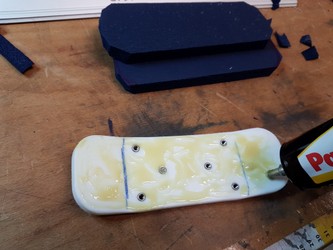
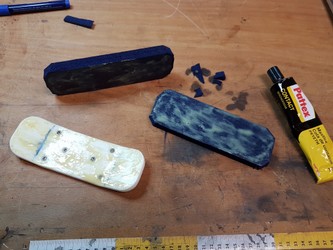
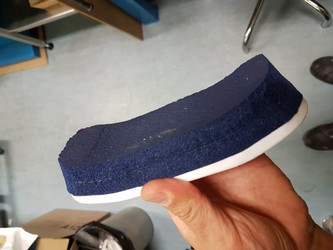
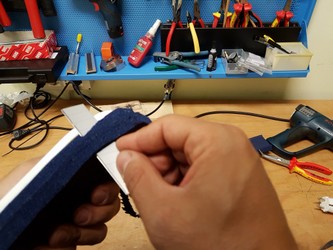

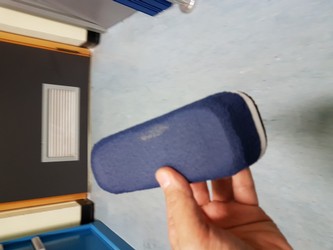
Ora proviamo a cucire una fodera di finta pelle.
La si può acquistare in qualsiasi negozio che vende accessori per calzatura o in qualche Brico ben fornito.
Io ho comprato una striscia di ecopelle nera e un pezzetto di cuoio, spesa totale 6 Euro.
Iniziamo con il prendere le misure dell'ecopelle e tagliarla per creare il cuscino.
Cucite i bordi dall'interno e fissate i bordi con della loctite .
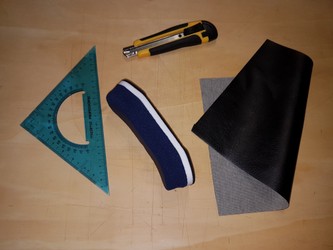
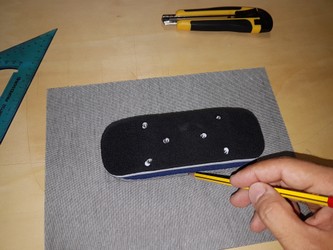
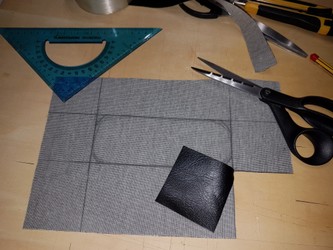
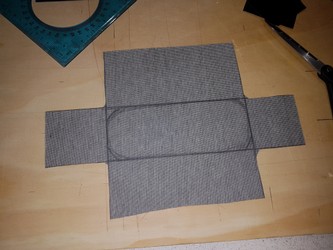
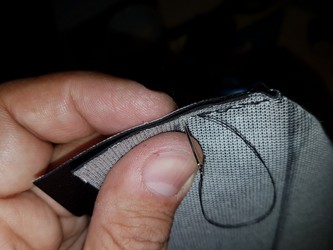
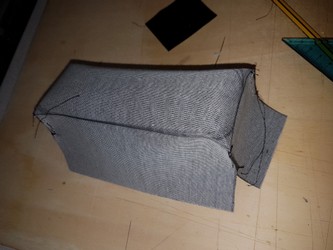
Proviamo ora il nostro cuscino sulla sagoma imbottita : deve entrarci con un po di sforzo per far si che venga tirata bene!
Lasciatela una giornata in modo che prenda un po la forma.
Successivamente toglietela e ricoprite il sellino con 2 strati di pellicola trasparente ( quello per il cibo per intenderci ). Applicateci sopra la vostra forma di ecopelle e tirandola per bene fissatela alla lastra con una sparapunti.
Tagliate via il film di pellicola trasparente in eccesso .
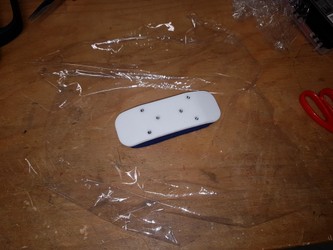
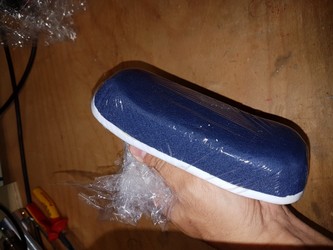
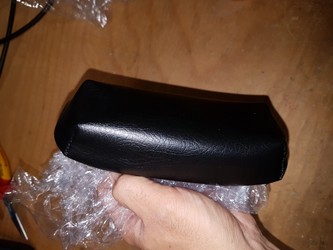
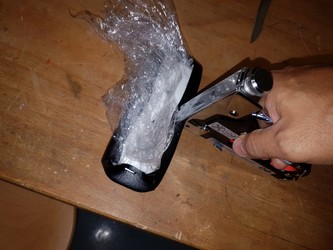
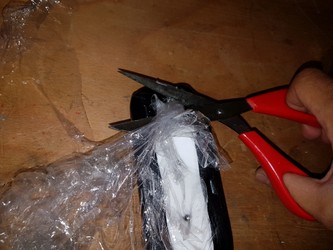
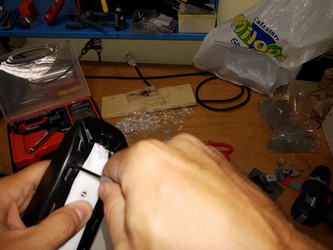
Ora con un bulino tracciate i fori rimasti coperti dall'ecopelle e scoprite la foratura con una fustella.
Ritagliate una forma uguale alla lastra di cuio con la foratura già fatta e applicatela sul retro del cuscino con del mastice da calzolaio , premendo bene le superfici.
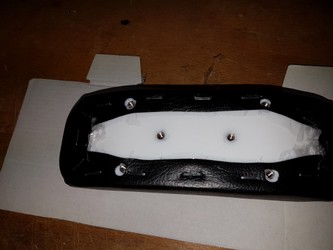
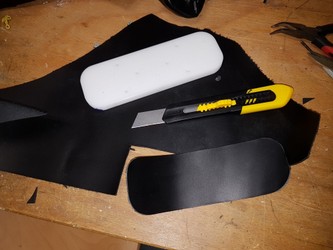
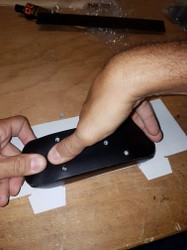
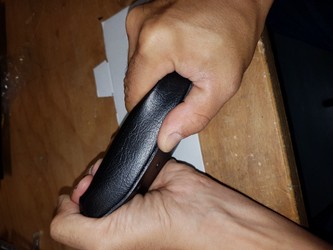
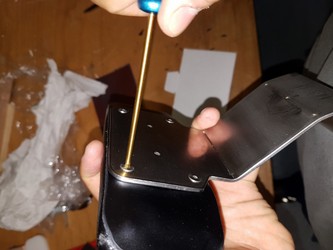
Bene! abbiamo finito.... ora si può motare il tutto!
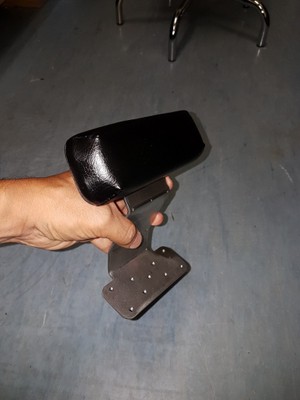
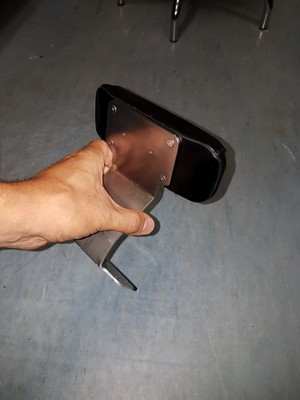
Informazioni tecniche per la realizzazione
Puoi trovare misure, disegni e file necessari per la realizzazione.
Di seguito riporterò le varie modifiche che sarebbe meglio apportare al progetto, dopo un pò di test...
Se avete idee o dubbi o consigli non esitate a scrivermi : info@sma73.it